Services
Our specialty, we have been manufacturing custom wiring harnesses and cables for OEMs, panel builders, controller boxes, engine harnesses, custom machinery harnesses and other custom manufacturers who use our wiring harnesses in their products.
C-T Wire Prep Inc. is known for its enhanced level of quality as a wire harness component manufacturer as seen in the solar industry during the Canadian government grants program.
Our tooling library allows us to fit most common connection systems.
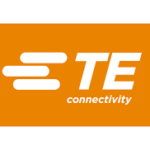
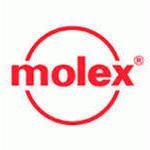
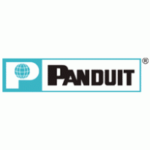
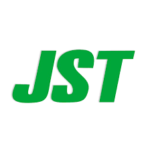
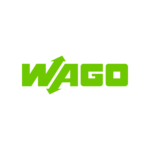
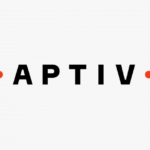


Wire Cutting & Stripping
C-T Wire Prep Inc. uses high precision Artos cutting machines that are semi-automated to cut and strip wires from 4-28 AWG. Cut specifications can be as tight as 1/32" tolerances or less if required.
Many styles of wire to choose from including:
-
- TEW (ul 1015)
- TR-64 (UL 1569/1007)
- CL1251
- THHN
- SJOOW
- CL1503/UL3321
- multicore
- any ratings
- tinned/bare
- pre-fused/stranded
**More types available please call the factory to inquire**

Hot Stamp Marking
Hot stamping is a precision process to apply labelling to wire ends in an automated fashion in-line. A powder-coat type ink is pressed by heated letter wheels against the wire insulation to transfer characters permanently onto the wire.
Robust quality monitoring during the manufacturing process ensures that stamps do not damage the wire insulation and create unsafe power leakage conditions.
Although this method has been banned in aviation wiring, it still remains the best option for applications requiring tight spaces or low profiles.
Custom Jig Builds
Each custom harness build has a specific set of unique requirements to build. Our Process and Engineering teams work together to make sure each product can be built fast, efficiently, and repeatable to maintain the highest quality levels
Creating a custom wire harness build jig is somewhat of an art. The engineering team's aim is to replicate the exact environment in 3D form to account for any routing requirements of a wire harness and any placements, breakouts, etc.
Most often, our team does an on-site physical analysis of a product to obtain the physical requirements and calibrate our custom Jigs. This includes measuring physical wire lengths, connection points internally to devices, limitations to design due to space requirements and more.
Once specs are obtained, a physical recreation of the routings needed on the final product are developed and a sample prototype is produced to be tested for fit, form and function.
Tin (Solder) Dipping
Tin Dipping was invented originally as a means to make steels and other metals resistant to corrosion for ironware and canning. The idea was adapted to the use of tin in the electronics industry to do the same.
Similar to electroplating, tinning involves heating a metallic substance to bond it with the one it will coat.
Flux is used as an adjunct and gets its name from the movement it creates when it is heated by "pulling" the metals together.
Although other connection means are available for some applications like ferrules for panel building, tin dipping is still widely used in the wire industry as a way to solidify inner strands, prevent corrosion in harsh environments and strengthen stripped wire ends for binding posts, twist-ons or terminal blocks requiring further soldering.
At C-T Wire Prep Inc. as part of our committment to environmental transparency and being RoHs, we use lead-free raw solder in our processes
Single Wire Stripping
Different types of wire and applications require different stripping solutions depending on their type. During the cutting process, wires are stripped automatically.
When a strip is performed at a different stage of the production process, special tooling is needed to reach the same quality of strip equal to automated stripping. We have the following specialty stripping tooling available at C-T Wire Prep inc:
- Schleuniger mini-strip
- Schleuniger MP257 multi-strip coaxial
- Artos AM-2 heavy gauge/ cable stripper
- Kames Tool for Convoluted Cable Stripping
Fully Automated Lead Processing
Simple single-ended or double-ended hookup wires can be processed at higher run rates and cheaper costs by using fully automated tooling. We have capabilities to run most of our applicators on our automated tooling to serve the high volume wire industry.
Get A Quote