Creating a new assembly process when on boarding a brand new custom product line involves many important aspects. In order for manufacturers to maintain profit margins, scalability and repeatability in their processes, critical planning of all the necessary physical components is needed to execute a successful product launch with a client.
The following areas are essential when beginning to map out an assembly process.
- Space planning
- Benches & assembly Platforms
- Permanently Fixed Tools
- Jigs & Fixtures
- Portable/Handtools
- Station Organization
- Employee Ergonomics
- Performance Metrics Data Tracking
- Process Analysis & Innovation
- Inline Testing & Repair Loop
The ultimate objective is to get from raw materials to a final assembled product ready for shipping in the least amount of time and at the highest rate possible while maintaining perfect quality.
Space Planning
Careful consideration of product assembly flow and worker traffic is important at this beginning stage to ensure that the entire assembly process can be completed efficiently without wasting valuable factory floor space.
Line automation is often used to move WIP parts down the assembly line, but sometimes due to a product’s size and the way assembly processes and in-line tests require connections, workers must move around machinery to collect parts. Trays, bins or engineered parts holders make the most sense to move them safely and efficiently.
Pathways for foot traffic must be mapped out and included in the total space requirements prior to launch to ensure no bottlenecks are created in product movement.
In some types of manufacturing, different models of design are used to move products through the assembly process. Often, a factory will have one or more “cells” which is a small area of floor space that completes a specific sub process to the overall assembly process and then injects those parts into the line flow of the main process. Designing assembly lines around cells can be a challenge. It may also mean that during the main assembly flow, the WIP product may leave the process flow to be sub-processed inside a cell and then entered back into the process flow later for further assembly.
Benches & Assembly Platforms
Once a suitable space is designated for construction, analysis of the entire planned build is done to determine how many stations and sub processes the line should be broken down into. A critical step here is to list all tools, processes and jigs & fixtures in order of when they are needed in the process. Once gathered, it can then be split into station sub assemblies. Many times multiple build aspects are completed at the same station before a WIP product moves onto the next station. Other times, due to specialized needs and time constraints, the station may only be capable of completing a single task.
Permanently Fixed Tools
It is always good practice when designing an assembly line to attempt to fix the needed tools to a specific assembly station. This helps to keep employee transitions between stations flowing smoothly and also to help repeatability in the worker’s motions as they complete the process. Hand/muscle memory comes into play here where a commonly placed tool becomes an extension of the worker to increase efficiency.
Common tools are hung from retractable hanger devices for easy use in front of the worker or easily accessible to quickly complete their assembly. Some tools include electric drivers, cutters, lifts, air tools and automation controls.
Hand tools such as tweezers, side cutters, insertions tools, extraction tools and other special engineered hand tools to assist product assembly are common to most assembly line processes. Some of these tooling items are considered consumable and are provided as needed to employees, but usually specialized hand tools stay at the station they are used.
Shadow boards and other tabletop space designations help organize stations for repeatability and speed.
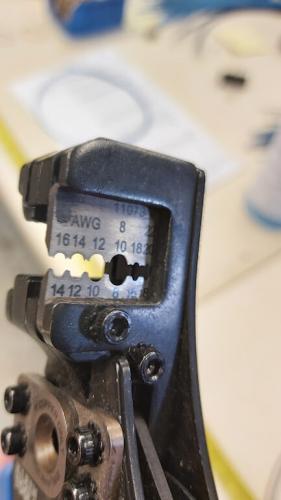
Jigs, Fixtures & Hand Tools
Jigs and fixtures are used in some way during nearly all assembly processes. Table space must be considered to allow for proper operation of moving levers, hinges plungers, springs and other connection types for efficient completion. Often jigs are affixed directly to a station surface so that it does not move during use.
Learn more about jig & fixture design here
Station Organization & Employee Ergonomics
Employee health and their ability to maintain production rates safely should come first when organizing any assembly station. Range of motion, angle of operation, comfortability and tooling organization are key aspects to analyze when innovating processes to help line workers perform at their best.
The best application of this is to limit the worker’s motion to a minimum to conserve energy and design processes so that WIP can be handled the least number of times while being manipulated. Listening to your employees for recommendations often helps innovate station efficiency during use.
Tracking It All
In order to innovate the assembly process and increase production rates, proper data tracking is needed to analyze performance. Time studies are used to come up with average run rates for each station. Once rates for each sub process are established, station level production times can be analyzed. When disparities arise in station process length, the process can then be modified by moving smaller sub processes back a station or forward to even out the time differences and create sustainable WIP flow.
Inline Testing & Repair Loop
During the assembly process, it is a good idea to implement tests on the partially assembled components to remove defective parts and worker errors. In the wire harness industry, tests and quality checks may come in the form of first off wire spec visual checks, an electrical continuity test, Hipot test, resistance analyzation, crimp height & pull testing, crimp inspection, housing insertion orientation visual inspection, overall product cosmetic inspection.
Repair Loop
When inspection stages are added into the assembly process, quality can be increased by removing failed parts to a temporary segregated area beside the line. Once separated, repair technicians or line workers can take the time to correct the errors during down time or off line and re-enter them into production at the same spot they were when they failed. Multiple repair loops can be built into the assembly process to achieve the greatest improvements.
Conclusion
Planning is everything when designing an assembly line process. If the necessary steps are taken, efficient floor plans can be easily developed to ensure high factory productivity, profitability and longevity.
We hope you found this information useful