Wire ends have always required identification in some form in order for visibility in control panels, interconnect points and for installers to correctly identify their circuitry.
Hot Stamping
An older method of marking still in use today in many industries, but with caution in the commercial wire industry is Hot Stamping. This method of marking involves some type of heated die and a transfer foil. The foil is placed between the item being marked and the die. The die is then pressed against the foil superheating the transfer substance onto the object. Correct precision pressing force during the operation transfers the “ink” to the surface of the wire without damage.
You have likely seen and used products that have been hot stamped. For example, here’s a Bic brand pen:

In this case, the hot stamping machine purposely injects the transferred image into the plastic surface creating an embossed texture.
When working with certified electrical wire labelling, hot stamping has its limitations due to physical size and its static position. standardly, up to 10 characters can be printed per end of a wire. The cutting machine interface makes sure that each wire cut/strip is performed in the blank space between the 2 stamped sides. Although stamps can be repeated along the surface of a wire, they cannot change during the operation or change the placement positions once the operation starts.

Additionally, clear heatshrink can be applied over stamps to further protect them in harsh environments.
From Shirts with Gold lettering to book covers, boutique chocolates in little boxes to official certificates sealed with a gold marking, hot stamping is used all around us on commercial products.
Restrictions For (WHMA-A620D Class 3) Products
In the wire industry, hot stamping has been used for many years as a low profile means of identifying wire ends. This I.D method has come under much scrutiny due to quality issues and improper processes. Due to this, they cannot be used in class 3 products such as aerospace, military and medical. Other methods for marking defined below are used in its place, and depending on application and environment, may be a preferred option.
Quality Monitoring
Quality must be monitored in real-time when using hot stamping as a wire marking method because of the fragility of the insulation we apply the markings to. Due to the need for high heat, precision placement using die inserts, and air pressure to mark the wire, the soft insulation of some wire types may be breached if improperly stamped.
Visual inspection of all markings is required to maintain insulation surface viability. At C-T Wire Prep Inc. we use customized quality plans based around ISO and IPC/WHMA – A620D which state no more than 20% deformation of wire insulation for quality products. We strive for 0% to offer the highest quality products available on the commercial market.
Inkjet Marking
A newer form of labelling/ identification is inkjet marking. In some cases, it took the place of hot foil stamping, but also has other specific uses. Over the past 20 years, massive improvements have been made in the technology of digital marking devices. Automation and innovations to ink nozzle system reliability have allowed for adoption into many industries.
In the wire industry, inkjet marking is the most commonly used solution for wire mills printing certification data repeatedly onto long runs of wire. Custom inkjet systems are also available for inline processing of wire ends much like hot stamping.
An inkjet marking system uses nearly the same technology as a standard inkjet printer for home office use, but uses specialized dyes and chemicals to create colors and to adhere to different insulation types. A specially engineered low profile print head is placed along the wire while it is being fed into the cutting machine.
Digital interfaces between the cutter and marking machine work in concert to make sure the wire marking is applied at the right spots where programmed and can be repeated indefinitely along the wire surface. This feature surpasses the abilities of a hot stamping machine due to the static nature of hotstamping.
Heat Shrink Labelling
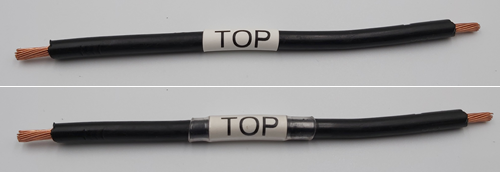
In harsh environments outdoors, or applications where liquids or chemicals are present, standard marking methods fail due to ink/foil loss and in some cases being physically removed from the wire.
Alternative marking methods are used commercially to securely identify wire ends in a ruggedized form.
Heat shrinkable labels are printed using thermal transfer printers which are then applied to wire ends and shrunk onto its surface. Typically, another clear tubing heatshrink is also applied over the label to seal the ink and further offer resistance to liquids and other harsh chemicals.
As a whole, marking solutions have not changed much since their inception, but innovations to the machinery and processes have in fact increased their quality. Not only has the quality of the identification markings themselves increased with better techniques, but the overall integrity of the wire insulation has improved, as well as use of more environmentally friendly materials.