One of the main challenges that engineers face in the custom wire harness industry is the multitude of different connection systems available on the market. There are literally thousands of different types of connectors and their respective terminals will only fit the matching housings. This poses “pressing” questions (no pun intended!)
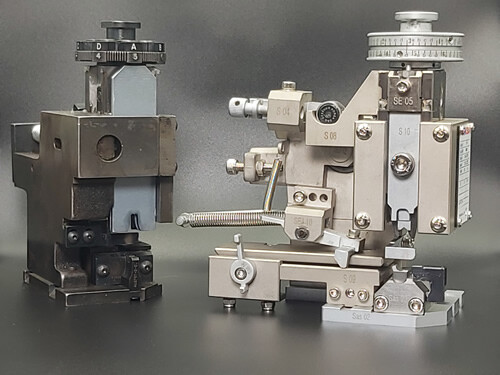
1. Which types do any given professional wire harness manufacturing facility have tooling for?
2. Which type are the best?
3. Most cost effective?
Part of our job at C-T Wire Prep is to first educate engineering teams responsible for sourcing connection systems for their new products about availability of processing tooling before they select one.
Each connection system use very specific tooling for their brand of component, so deciding on which is the best quality for certified products is vital for us as a manufacturing corporation and has many quality implications. TE Connectivity (formerly AMP/Tyco) has for many years been at the top of the industry competing for the market share on connections in the electrical industry. We found that AMP model G series presses and their mil-spec dies produced the highest quality component finishes for high grade uses, and so have added to our repertoire of tooling dies of that brand over the years.
Our goal is always to provide cost effective solutions to customers with long term reliable quality, and so we took the time for you to vet the best ones. We aim to provide every type of connection from F style metal formed terminals to fully insulated, weather sealed and military grade.
Unique applications sometimes require a different brand of connection such as Molex, Panduit, JST, or Packard for example, so special applicators must be used to crimp during semi-automated production. We have had many custom designed applicators made for the G press to crimp other brands of contacts at the same high quality.
All mil-spec crimp dies use perishable tooling inserts that wear over time and must be replaced. The Crimper (top “m” shaped piece) and Anvil (bottom floor step piece) combined, create the very specific shapes required for strength, durability and longevity of crimped contacts to wire.

As part of certifying a die setup for use on CSA and UL products, destructive pull testing is religiously performed per setup to test each and every time a die is placed into a press for use. This guarantees the absolute highest rate of quality per batch of goods produced.